Service-Free Fire Extinguishers
Why traditional fire extinguishers need servicing
Most traditional fire extinguishers consist of a steel cylinder with internal lining to prevent the fire extinguishing agent causing corrosion. The lining, however, regularly suffers from detachment from the main body as well as pitting which both can lead to corrosion. Corrosion in highly pressurised extinguishers is, of course, dangerous. Other potential failure points are the gauge needles which can get stuck and external dinting of steel extinguishers, which can lead to uncontrolled pressure release.
The only way to control these risks in traditional extinguishers is to have servicing engineers inspect and maintain the extinguishers, usually once a year (in other countries such as Germany every other year). The engineers can verify the free movement of the gauge needle and inspect the extinguisher externally for damage. However, the internal inspection requires the extinguisher to be discharged first, a very costly and wasteful exercise if it were to be carried out annually.
The British Standard for steel extinguishers instead specifies a discharge test with subsequent refill every five years. While this can be carried out at a customer’s site (if service engineers have discharge receptacles on their vehicle), many service companies simply scrap the extinguishers after five years and replace them with new units; a practice clearly not in line with today’s environmental priorities. The engineers then invoice the customer for the visit, a handling charge, the recycling charge for the old extinguisher and the price for a new extinguisher plus commissioning of the new extinguisher on top! This approach is costly to the customer and environmentally damaging.
Why P50 fire extinguishers are different
About 10 years ago Britannia Fire, an extinguisher manufacturer in Ashwellthorpe, Norfolk came up with a better concept. They are manufacturing a composite extinguisher that overcomes all the pitfalls of traditional steel extinguishers and as a result does not require servicing.
The P50 extinguisher consists of an inner, extruded plastic cylinder containing the chemicals. The material of the container is entirely inert, meaning that it cannot react with any of the chemicals contained, an essential feature if you want to avoid the chemicals in an extinguisher to age.
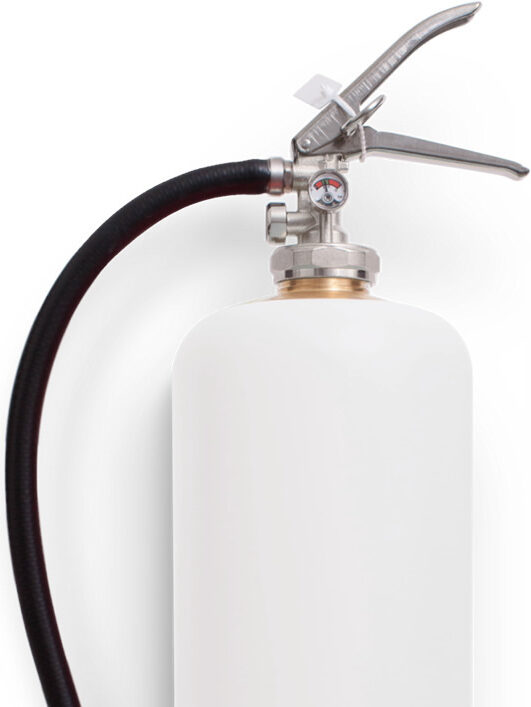
This cylinder is then cocooned in aramid fibre (as used in stab vests) to hold the pressure of the charged extinguisher. The technology stems from the manufacturing of propane gas cylinders and has been perfected for the use on extinguishers. The cocooned cylinder even has a designed failure point, should the pressure ever rise about safe levels, e.g. if the extinguisher should overheat. This guarantees that, unlike steel extinguishers, a P50 will never explode.
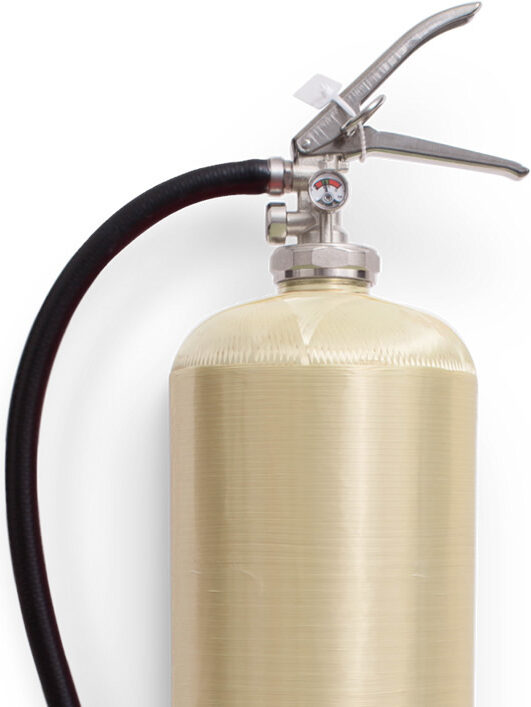
Both the inner cylinder and the aramid cocoon are then encased in an outer red plastic cover which prevents cuts, UV light and chemicals from attacking the inner components.
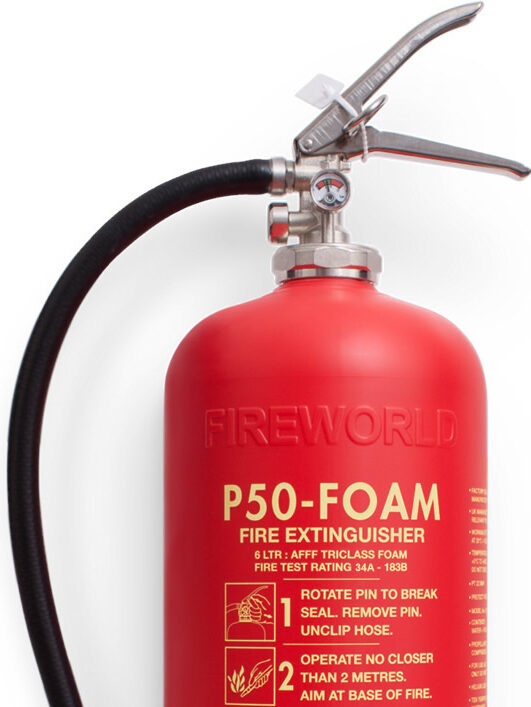
Nickel-plated brass valves, a permanent hose and a plastic foot round off the construction. The cylinder is then filled with the extinguishing agent and is pressurised with inert nitrogen gas. The chemicals are such protected to last a minimum of ten years.
P50 extinguishers should be installed by competent service engineers to ensure that the correct fire fighting cover and the correct fire point locations are chosen. Britannia’s main partner, Safelincs Ltd, offers the site survey, install and commissioning free as part of the purchase of P50 extinguishers. Their engineers will commission the P50 extinguishers and then train the customer in carrying out simple visual inspections.
Beyond that first install the extinguishers do not require any maintenance for ten years. As the extinguishers cannot corrode, no internal inspection is required. Hence there is no costly discharge required after five years, halving the use of chemicals. The P50 extinguisher does not dint and the cylinder head of the P50 has two pressure gauges to overcome the issue of stuck gauge needles. The gauge needles can even be ‘wiggled’ with a magnet which is attached to each extinguisher, to verify the functioning of the gauges.
The result of the customer’s own visual inspection is recorded in the fire safety logbook the customer uses for all their fire safety activities and the annual visual inspection is marked in the relevant fields printed on the back of the extinguisher.
After ten years in the field the extinguisher is then simply factory refurbished and can then be used for another ten years.
The lack of annual service visits and the fact that no discharge test is required after five creates huge cost savings for the customer and huge benefits for the environment.
Categories:Fire Safety Equipment
August 20, 2021[Last updated: August 20, 2021]
Comments are closed here.